Creating a Bill of Material
A bill of material contains information on the parent item, components, attachments, and descriptive elements.
You can create an engineering, manufacturing, or asset (maintenance) bill, copy an existing bill, or reference a common bill. When you create a bill, it exists only in the current organization. To use a bill in another organization, you must either copy it or reference it as a common.
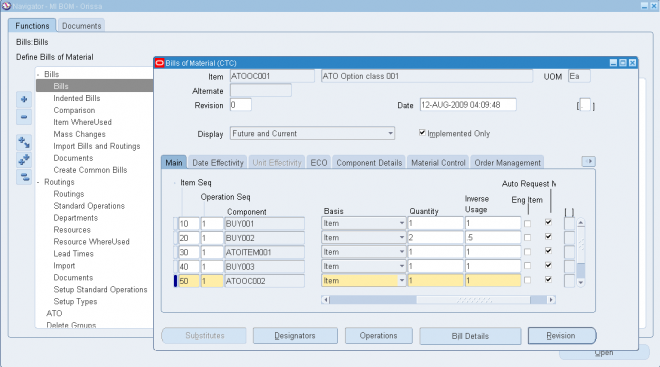
1.1. Enter the parent item for which you are creating a bill, and if you are creating an alternate bill, enter the alternate.
1.2. Enter or select the revision and the revision date.
1.3. If you are updating or viewing a bill, use the Display poplist to display all, current, or future and current components effective as of the revision date you specify.
Reference designators are used in BOM. Different RD are attached to different components in a BOM which are not lot based. RDs are comments and instructions for a particular component with business information in it.
Example : Item 001
Component 01 RD : U1
Component 02 RD : C2
RD : C2 means capacitor from supplier xyz.
Main TAB
2.1 Enter the item sequence, operation sequence, and the component item.
Item Sequence Field
The item sequence indicates the sequence of the item on the bill. It is used to sort components on reports and when choosing options from a model bill in Oracle Order Management. This defaults to the value of the highest existing component item sequence plus the value of the BOM: Component Item Sequence Increment profile option. If this profile option is not set, the default is 10. You can override or change this number.
Operation Sequence Field
Every routing carries operations. You can use the Routings form to assign operations to routings. Each operation must have a sequence number called the Operation Sequence Number.
On a bill, the operation sequence indicates the order in which you perform operations on a routing. You can have the system automatically generate Operation Sequence Numbers using a user-defined increment factor. A profile must be created where you can indicate how much the Operation Sequence Number will increment every time a new operation is generated. You can change the generated value if necessary in the Routings form. Valid values range from 1 to 9999999.
You can assign any component to any operation on the routing, including all components to the same operation (such as the first operation). The planning process assigns material requirement dates based on the operations to which you assign each component. You can define bills of material for items with or without routings. If you use routings, you can either define the bill first or the routing first.
With component-to-operation assignments, you can schedule and issue component material to the operation that requires the component on the exact requirement date. You can also assign the same component on the bill to different operations on the routing, with different usage quantities for each assignment.
If no routing exists for the item, all components default to operation sequence 1. You cannot change this value until you define a routing for the item. After you define the routing, you can update your bill of material with routing operations if you want specific component-to-operation assignments.
If you define the routing before you define a bill, assign components to valid routing operations, or an operation sequence 1 when you define the bill. If you define an alternate routing and then define the alternate bill, you can assign components to the alternate routing operations. If you define an alternate bill and no alternate routing exists, you can assign components to the primary routing operations.
2.2 In the Basis field, select whether the quantity of the component used is a fixed amount (Lot) or increases linearly along with the quantity produced (Item). If the component quantity required increases or decreases linearly along with
changes to the work order or job quantity, then select Item. If the component quantity required remains the same regardless of the work order or job quantity, then select Lot.
Basis Field Constraints
- You can define the Basis field as Item or Lot for mandatory components in an ATO Option Class or an ATO Model bill of material.
- You can only define the Basis field as Item for option items, option classes or submodels in an ATO Option Class or ATO Model bill of material.
- You can only define the Basis field as Item when the WIP Supply Type is Phantom
2.3. In the Main tabbed region, enter either the Quantity or Inverse Usage used to make one unit of this assembly item at the current operation.
The Inverse Usage field calculates a fractional quantity for you in the Quantity field, to 42 decimal places. Use the Quantity field when the quantity used is a whole number. Use the Inverse Usage field when the quantity used is a fractional number. When you enter a value in either field, the system automatically calculates and populates the value in the other field. Inverse usage is also available using Work in Process, Shop Floor Management, and Product Lifecycle Management.
The Quantity and Inverse Usage fields can include negative or decimal values, subject to the following rules:
- Pick-to-order bills cannot have fractional component quantities if Oracle Order Management is installed.
- Pick-to-order option class components cannot have negative values.
- Components with Check ATP turned on cannot have negative or zero quantities.
- If the component has Quantity Related turned on, then the component quantity cannot be fractional or negative.
- If an implemented component has Quantity Related turned on, then the component quantity must be equal to the number of reference designators.
1. The planning process in Oracle Master Scheduling/MRP ignores negative requirements on standard discrete jobs and components with a negative usage on a bill of material when netting supply and demand.
2. If you enter a negative quantity for a component, you should enter either Assembly pull or Operation pull for the supply type to ensure that you transact the material when you build the bill.
2.4 Select Auto Request Material to automatically create move orders or purchase orders for the component item.
question
HI
how i can setup system that Auto request material doesnot been selected by default
regards
razie